By Bruce Geiselman
Manufacturers of a diverse array of products — everything from aircraft parts to orthotics — are beginning to reap the benefits of 3-D printing for industrial-level use. Printers make it possible for them to lightweight their products, producing parts that previously might only have been made with metal, or through injection molding.
However, experts say manufacturers are still only scratching the surface of what is possible. As companies such as manufacturers of auto and aircraft parts have embraced 3-D printing, exploiting its potential for lightweighting starts at the beginning — with part design.
Jumping on board
Manufacturers in the automotive and aerospace industries have been among the early adopters of 3-D printing as a way to reduce part weight, say representatives from 3-D printer manufacturers Carbon, EOS, Arburg and HP.
In some cases, 3-D printers can make plastic parts previously only possible with metal, said Fabian Krauss, global business development manager for EOS of North America. He estimated that a part made by 3-D printing might weigh between 10 and 20 percent less than one that is injection molded. And, he said, “The percentage of weight savings going from a metal to a plastic part can be larger than 50 percent.”
Airplane makers like Boeing and Airbus have taken notice, adopting 3-D printing to make parts such as air ducts. However, a reduction in weight may not be the sole or even primary consideration.
Manufacturers are increasingly turning to 3-D printers to produce complex parts, including ducts for automobiles and planes.HP Inc.“Some can be quite large and very complex, and typically they are built in multiple parts,” said Terry Wohlers, principal consultant and president of Wohlers Associates, an additive manufacturing consulting company. “You’d be molding these things, tooling for every part, and then you’d have to assemble them.”
3-D printing air ducts can consolidate two parts, or five parts, or even 25 parts into a single part.
“Obviously, for every kilogram of weight you can remove from a plane, you have dramatic cost savings in terms of fuel economy and environmental benefit,” Rolland said.
Car makers also are cashing in.
For instance, Carbon has been working with Ford on making parts for production vehicles. In one case, a part produced by a Carbon 3-D printer replaced a metal bracket for a parking brake. The change resulted in a greater than 60 percent weight reduction. In another example, 3-D printing a Lamborghini gas cap resulted in a 14 percent weight savings compared with an injection molded alternative, Rolland said.
A fresh outlook
For other manufacturers, though, 3-D printing might still seem like a novelty.
As a lightweighting approach, Wohlers acknowledged 3-D printing has been “a little slow to take off in a big way.”
“It’s compelling and interesting and exciting and all of those things, but those things aren’t necessarily enough to push you over into this new area because you also have to do a cost justification, and that can be terribly difficult to do, to compare the old vs. the new,” he said.
Full-scale adoption of 3-D printing requires a change of mindset for manufacturers accustomed to more traditional techniques, experts said, because the rules for designing lightweight injection molded parts don’t necessarily apply to 3-D printing.
“It’s one of the really interesting challenges that we face, which is to get people in the mindset of thinking about what’s possible to do with 3-D printing, in particular as it relates to lattices and lightweighting,” Carbon’s Rolland said.
Lightweighting through 3-D printing may save material costs, but manufacturers must consider whether those savings outweigh the expense of the design tools and training.
“It’s not natural or automatic for the current workforce to do this, and it requires at least two things,” Wohlers said. “One is a rethinking or a new way of thinking, and then you need software tools to support those ideas.”
To meet the challenge, representatives of printer OEMs said their companies provide expert consultation, as well as software to help their clients realize the full benefits of 3-D printing.
For instance, Carbon has developed software to determine the most effective lattice structures for lightweighting.
The lattice and honeycomb structures that can be produced by 3-D printers are ideal for lightweighting production parts, such as helmets.HP Inc.The software produces design iterations to determine the best structure, based on the characteristics of the material and desired properties of the final part, Rolland said.
Using machine learning, the software can “navigate through really complex geometric lattice space in order to find the optimal solution,” he said. This eliminates the need to repeatedly redesign and print a part.
Wohlers said software has improved to help parts designer take full advantage of 3-D printing. Numerous companies have introduced software that designs lattice structures and performs a finite element analysis, he said.
“The most recent versions of the software will put a load on it,” Wohlers said. “It’ll have finite element analysis built right into it, and it’ll analyze to make sure that it can withstand the load ... that’s applied to it.”
Inspired by nature
Another means of lightweighting 3-D printed parts is the use of bionic structures, also known as biologically inspired engineering or topology optimization.
“Nature, for example, could serve as a model for bionic design or optimization of existing applications,” said Martin Neff, head of Arburg Plastic Freeforming. “The idea is to pack the material exactly where the force flows and to dispense with excess material elsewhere.”
Martin Neff, head of Arburg Plastic Freeforming, sees opportunities for 3-D printing to help manufacturers further lightweight parts.Arburg IncUsing this approach, he said that the precise areas of a part that experience higher levels of stress could be reinforced, for example with glass or carbon fibers, while others are produced with smaller quantities of plastic.
Bionic structures mimic structures found in nature and can be strong while reducing overall material use. An example is a tubular or hollow object designed to have a structure similar to bone. Bionic engineering involves analyzing a part to determine where it needs to have thick walls and where the walls can be thin to reduce weight.
Designed to be better
David Woodlock is an application, development and design manager for HP, which last year worked with Bastian Solutions, an Indianapolis-based materials-handling systems integrator, to design and 3-D print a robot from plastic. It had previously been made from metal.
“Our customers don’t necessarily have all the experience, all the licenses, all the time to invest in learning all these new tools, at least originally,” Woodlock said. “We help them do that … We’re always scoping out all the new design software out there. We get familiar with them, and we can help customers through that whole design process, kind of utilizing the new-to-world techniques and software that’s out there.”
Shoe orthotics can be 3-D printed with a lattice structural that makes them lighter, as well as more flexible.Wohlers Associates Inc.Tools for designing for 3-D printing include software for topology optimization, computational fluid dynamics and developing lattice structures, he said. These are areas in which many companies lack experience.
“We help them use those tools and bring them up to speed on those tools,” he said.
With the help of HP and another partner, Bastian Solutions used HP Multi Jet Fusion and Carbon M2 printers to 3-D print 45 percent of the arm of its robotic Bastian Solutions Shuttle System. The components include the robot’s fingers, joints and elbow. HP’s technology allowed the company to swap out metal components for ones made with a proprietary HP nylon resin filled with glass beads.
“Now, their final product is a lot lighter,” Woodlock said. “What lightness means in industrial automation, robotics, is speed. … Having a lightweight robot, they can actually make that robot move faster, do its job faster.”
Other benefits
With the ability to tailor a product to its user, 3-D printers could fill a unique niche in manufacturing.
Wohlers pointed to some shoe orthotics he keeps in his office to show the benefits of 3-D printing. They have a lattice structure, but lightweighting is just one of their strengths.
Terry WohlersWohlers Associates Inc.“It’s partly to use less material and make them lighter, but also to give them a different type of flex property,” he said. “If you can imagine a lattice structure vs. a solid structure, you could widen the lattice and make it more flexible, and that’s what this company has done to achieve something that you couldn’t do by molding the inserts, which is the normal way of doing it.”
Carbon’s work with athletic-gear makers illustrates some of the possibilities. The company has partnerships with Adidas to produce 3-D printed elastomeric midsoles with lattice structures and Riddell to produce 3-D printed elastomeric helmet liners that replace traditional foam. In those cases, Rolland said, “you have athletes that want state of the art in protection, but lightweighting and ventilation is also super important. This is, again, where we see really exciting opportunities for lattice structures to have a big impact.”
He predicts more opportunities for lightweighting through 3-D printing.
“I think there is a lot of room to grow,” he said. “This lattice capability is really new. I think a lot of part designers aren’t even aware of it. That’s a big part of our multiyear plan, to educate people, give them access to our platform, show them examples of how it can benefit their industries. I think we’re just getting started, for sure.”
Neff also sees plenty of room for growth.
“The potential of additive manufacturing is often not fully exploited, which is why we still see a lot of room for improvement,” the Arburg official said. “Multimaterial, functional integration or even the combination of processes are mostly still in their infancy but are still part of this open-thinking process. As mechanical engineers, we want to work out the areas of application for additive manufacturing together with our customers, while making full use of the geometric freedom of design.”
Bruce Geiselman, senior staff reporter
Contact
Arburg Inc., Rocky Hill, Conn., 860-667-6500, www.arburg.com
Carbon, Redwood City, Calif., 650-285-6307, www.carbon3D.com
EOS of North America Inc., Novi, Mich., 877-388-7916, www.eos.info
HP Inc., Palo Alto, Calif., 650-857-1501, www.hp.com
Wohlers Associates Inc., Fort Collins, Colo., 970-225-0086, www.wohlersassociates.com
Bruce Geiselman | Senior Staff Reporter
Senior Staff Reporter Bruce Geiselman covers extrusion, blow molding, additive manufacturing, automation and end markets including automotive and packaging. He also writes features, including In Other Words and Problem Solved, for Plastics Machinery & Manufacturing, Plastics Recycling and The Journal of Blow Molding. He has extensive experience in daily and magazine journalism.
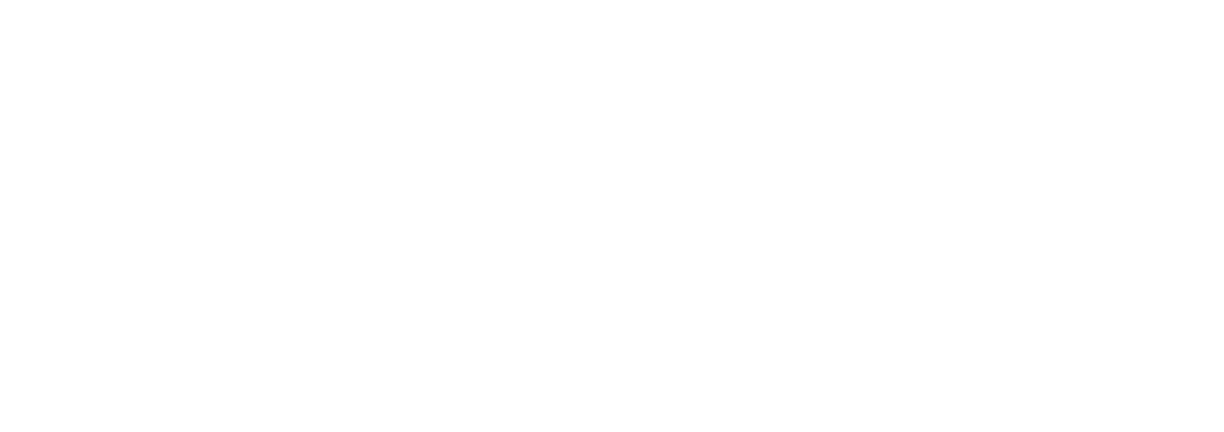