A new series of 3-D printers offered by Diabase Engineering includes a machine that combines additive manufacturing with CNC machining to produce strong parts with superior finishes.
The H-Series includes an additive-only 3-D printer, as well as a hybrid machine that combines 3-D printing technology with CNC machining. Both machines employ fused-deposition-modeling (FDM), meaning they have extruder heads that pull filament from a reel and push it into a heated cavity and through a small nozzle opening. They make parts that can exceed 15 inches by 7 inches by 7 inches.
The machines employ a rotary turret-style arm that can accommodate as many as five of Diabase's proprietary Flexion extruder heads, said Stephen Heston, manager of product development and an owner of the 3-year-old company. Flexion extruder heads having different nozzle diameters and using different material filaments can be mounted onto the turret. This allows a user to switch between large nozzles for bulk filling and small nozzles for detailing, or to print with multiple materials. Print speeds vary, depending on nozzle diameters, material type and desired part dimensions.
The Flexion extruder heads handle a range of rigid and flexible polymers, including ABS, polylactic acid, nylon, PET-glycol and TPU, as well as flexible materials, such as urethanes and elastomers. Materials with melting temperatures of up to 572 degrees Fahrenheit can be used.
The turret arm is designed so that only one tool is in contact with the part. Although the turret can index, the machine bed is also designed to move during manufacturing. The part bed moves left and right and back and forth according to the deposition or machining path.
Heston acknowledged that FDM printing has a reputation for producing parts with reduced strength and coarser surface finishes. He noted, though, that FDM has legitimate advantages over higher-resolution printing approaches. "Probably the most underappreciated and underutilized advantage is the ability to deposit multiple materials during a single build," he said.
HYBRIS MACHINING/PRINTING
Designed in a way that's reminiscent of a vertical milling machine, the hybrid machine is built to overcome such challenges. It has a cast body to provide rigid and accurate motions, and handle both machine accelerations and cutting tool loads.
In addition to its five primary positions — designed for either extruder heads or CNC tooling —the turret on the hybrid machine has five secondary positions for accessories, such as measurement tools.
With the machine's CNC tooling, users can smooth out the coarse surfaces of printed parts. In many applications, the resulting finish is of higher quality than a part made with a higher-resolution additive process such as selective-laser sintering, Heston said.
By alternating between additive manufacturing and subtractive manufacturing, the machines produce little waste and high outputs. The parts are accurate and exhibit high-quality surface finishes, Heston said.
A software program developed by Diabase combines the CAD/CAM designs for additive and subtractive manufacturing (even when different design programs are used), which simplifies operation, eases tool-path generation and allows for potential manufacturing errors to be identified prior to machining.
OTHER FEATURES
Diabase offers a variety of accessories for both its additive and hybrid machines. For instance, a removeable enclosure is available that helps to minimize the noise generated from CNC operations. The enclosure has vents for the exhaust of fumes or chips and air circulation.
Also available is an automatic nozzle-cleaning system that works when the extruder is inactive and out of contact with the part. The system, a solenoid-driven pincer with a pair of blades, scrapes excess material away from the nozzle tip, preventing material buildup that can generate printing errors or contaminate the part.
The company is evaluating the possibility of incorporating other, non-FDM additive deposition systems, such as liquid resin jetting and continuous fiber deposition.
Mikell Knights, senior staff reporter
Contact:Diabase Engineering LLC Longmont, Colo., 720-340-3539,
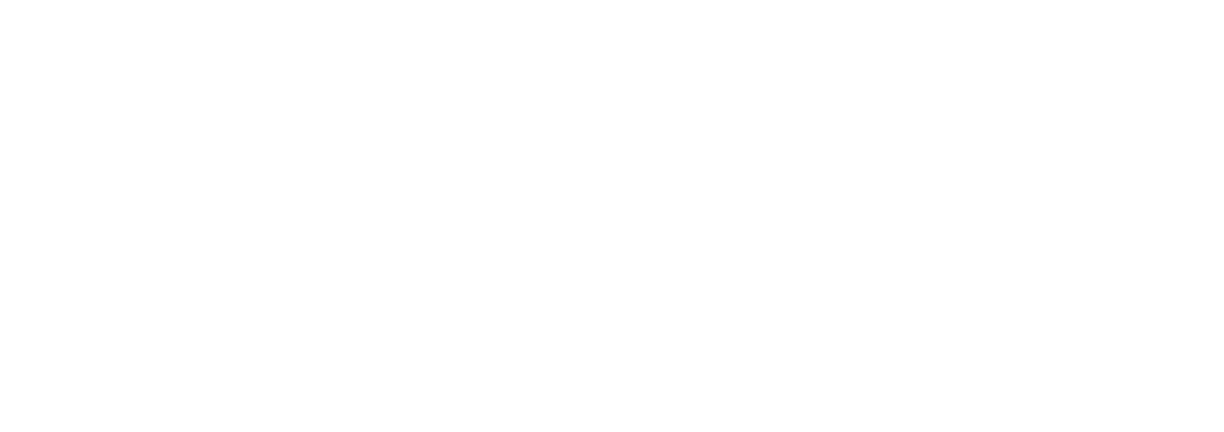