Stratasys Ltd., Eden Prairie, Minn., is expanding its additive manufacturing capabilities with two new technologies it's making available to its partners.
Exhibition models of the company's Infinite-Build 3D and Robotic Composite 3D Demonstrators were on display in September at the International Manufacturing Technology Show in Chicago. Though Scott Sevcik, director of manufacturing platform development for Stratasys, said the machines are not yet commercially available, he believes they offer great potential for industries such as aviation.
"We expect that we will be selling systems derived from these," Sevcik said.
Made for building large, lightweight, thermoplastic parts and tools, such as those used in the automotive industry, the Infinite-Build 3D Demonstrator is a fused deposition modeling printer. It boasts a unique design in which print jobs grow vertically, rather than in layers along a horizontal plane. The printer extrudes the initial layer along a support wall, which is then pulled away from the workpiece as the part gets bigger and can stand on its own.
Darryl Davis, the president of Boeing Phantom Works, which has used a Demonstrator to test its feasibility for producing low-volume, lightweight parts, said that the system offers promise.
"The Stratasys Infinite-Build 3D Demonstrator enables products to be made at a much larger and potentially unlimited length, offering us a breakthrough tool to add to our robust additive manufacturing processes," Davis said in a statement.
Besides the possibility of making bigger parts, the printer also can achieve speeds that have been previously unattainable, Sevcik said. As an example, he cited a composite layup tool that took just 23 hours to print; by comparison, he said, Stratasys' Fortus printers can take 10 times as long.
Speed is also one of the advantages he touted in describing the Robotic Composite 3D Demonstrator, which uses a multi-axis motion system to continually reorient workpieces, so no support material is required. Siemens AG, Munich, supplied the system's motion control hardware and design-to-printing capabilities.
The ability to constantly turn the workpiece allows the printer to create sophisticated workpieces quickly, Sevcik said. In one case, the robot, which is equipped with an extruder end-effector, printed a piece in 60-90 minutes that would have taken other systems 12 hours or more, he said.
The Robotic Composite 3D Demonstrator is made for carbon-fiber-filled thermoplastics, and has so far been tested using nylon, Sevcik said.
Parts made using the Demonstrators include tooling and custom aircraft panels.
Karen Hanna, copy editor
Contact:
Stratasys, 952-937-3000, www.stratasys.com
Karen Hanna | Senior Staff Reporter
Senior Staff Reporter Karen Hanna covers injection molding, molds and tooling, processors, workforce and other topics, and writes features including In Other Words and Problem Solved for Plastics Machinery & Manufacturing, Plastics Recycling and The Journal of Blow Molding. She has more than 15 years of experience in daily and magazine journalism.
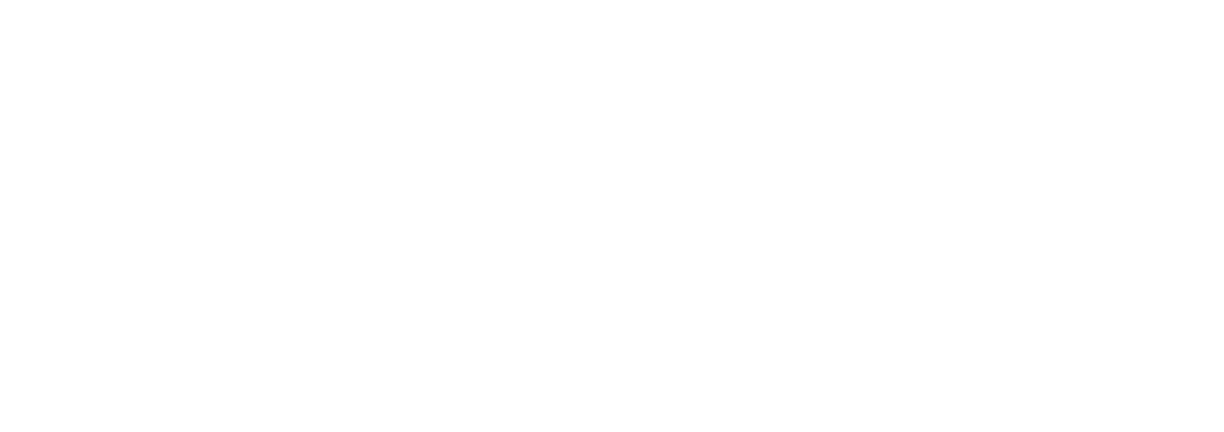