By Karen Hanna
The show must go on.
With no NPE, and in the midst of a pandemic, injection molding machine (IMM) manufacturer Tederic has shown that business marches on, as it introduced the Neo family of six machines: the Neo.T, Neo.E, Neo.Ec, Neo.H, Neo.Mv and Neo.Ms. The machines, with clamping forces from about 60 to about 4,400 tons, are equipped with a new generation of energy-efficient servo pumps that enable ultra-high response speeds. Compared with conventional hydraulic IMMs, the Neo lines use 30 percent to 80 percent less energy.
The machines, which made their debut in April at Chinaplas, won’t be available in the U.S. till late this year. They feature redesigned machine guarding and have been designed to be safe, practical and user-friendly.
“The Neo family of machines has been designed to offer a premium solution, with enhanced specifications, but still at a very attractive price. A full suite of technologies are available with the Neo,” said Tony Firth, the VP of sales and marketing for Tederic North America Machinery.
“Though there is a continuing drive for more sophisticated solutions, which Tederic is able to meet, many molders realize that the current labor shortages are creating a skills gap that is often best served by ensuring that the control is both friendly and relatively simple to use,” he said. “Controls will continue to evolve. Machine learning will become more important in a few years. But more advanced controls should not become more complex to use.”
The new machines have advanced Keba controls and touch-screen control monitors available in a range of sizes, from 12 inches to 21 inches, depending on the model. The controllers offer support for OPC, UA and Modbus data protocols and feature free programming capabilities to accommodate a variety of process requirements.
All the machines have larger tie-bar spacing than previous Tederic models.
In addition to their shared features, machines in the six new lines boast features unique to each series. The new lines are the Neo.E, Neo.Ec., Neo.T, Neo.H, Neo.Mv and Neo.Ms.
Of the new lines, one, the Neo.E, is all-electric with clamping forces ranging from 60 to 507 tons, injection speeds of about 1.6 feet per second and pressure accuracy to within 1 bar. The machines can be used for manufacturing closures and high-tolerance components for the medical, packaging and electronics end markets, as well as high-volume, thin-wall applications. They boast low-speed control and feature NSK linear bearing for platen guidance and the latest-generation motors and drives with DC bus technology. The machines come with a standard 15-inch control screen.
It’s “accurate, fast, rugged” and precise, Firth said.
With clamping forces ranging from 185 to about 1,200 tons, the Neo.Ec machines are appropriate for custom molding and capable of injection speeds of up to about 9.8 inches per second. They have electro-mechanically driven injection, screw-rotation and clamping-unit movements, along with an integrated power pack and servo-pump that power the ejectors, carriage and core pulls. The carriage has twin hydraulic pistons, and the moving platen features linear bearing guidance.
The Neo.T machines have clamping forces ranging from 99 to about 4,400 tons. New features include enhanced mold height and a special clamp-braking system to improve mold positioning accuracy. According to Tederic, they are energy-efficient and appropriate for custom molding.
The two-platen servo-pump Neo.H machines can be used by custom molders and manufacturers of a variety of parts, including automotive and appliance parts, as well as trash cans and totes. They are available with clamping forces ranging from about 750 to nearly 3,000 tons; eventually, they’ll top out at about 4,400 tons. They offer enhanced mold daylight, and a special clamp-braking system to improve mold-positioning accuracy. They use an electric screw drive, and the latest generation motors and drives with DC bus technology. Available options include tie-bar extraction, and extended daylight with mold side-loading.
Machines in the servo-pump-driven, multi-material Neo.Mv line have a Spinsure-V vertical rotary platen. “Injection units can be both servo-hydraulic or electric, or even a mixture of both types. Up to five injection units can be accommodated, with vertical, perpendicular, parallel and piggyback arrangements,” Firth said. Both hydraulic and electric injection units are available for the Neo.Mv machines.
Like the Neo.Mv line, the Neo.Ms line is designed for multi-material molding, with clamping forces ranging from 880 tons to 2,720 tons.
. The machines have two opposing injection units as standard, and additional injection units can be added as required. The secondary unit rides behind the moving platen.
Designed to rotate the center section of a stack mold, the Neo.Ms machines’ Spinsure-H horizontal rotary table is positioned between the fixed and moving platens. Rotary table movement and positioning are independently controlled, allowing for a range of mold designs and complex applications.
According to Firth, they “feature a horizontal rotary table with an upright ‘tombstone’ platen that rides on a sled positioned between the fixed and moving platens.” A second injection unit injects through the moving platen.
“Two molds are mounted, one for the primary material and one for the secondary,” Firth explained. “The rotation of the center platen transfers the mold half with the primary material component to the secondary material position. The advantages are that long parts can be accommodated in a smaller machine. Because the injection units are completely independent, the machine can also be used to simultaneously mold parts on two conventional molds.”
Karen Hanna, senior staff reporter
Vital Statistics
Model | Clamping-force range |
Neo.E | 60 to 507 tons |
Neo.Ec | 185 to about 1,200 tons |
Neo.T | 99 to about 4,400 tons |
Neo.H | 750 to about 3,000 tons |
Neo.Mv | 1,120 tons to 2,820 tons |
Neo.Ms | 880t tons to 2720 tons |
Contact:
Tederic North America Machinery Inc., Palmetto, Fla., 941-323-9081, www.tederic-na.com
Karen Hanna | Senior Staff Reporter
Senior Staff Reporter Karen Hanna covers injection molding, molds and tooling, processors, workforce and other topics, and writes features including In Other Words and Problem Solved for Plastics Machinery & Manufacturing, Plastics Recycling and The Journal of Blow Molding. She has more than 15 years of experience in daily and magazine journalism.
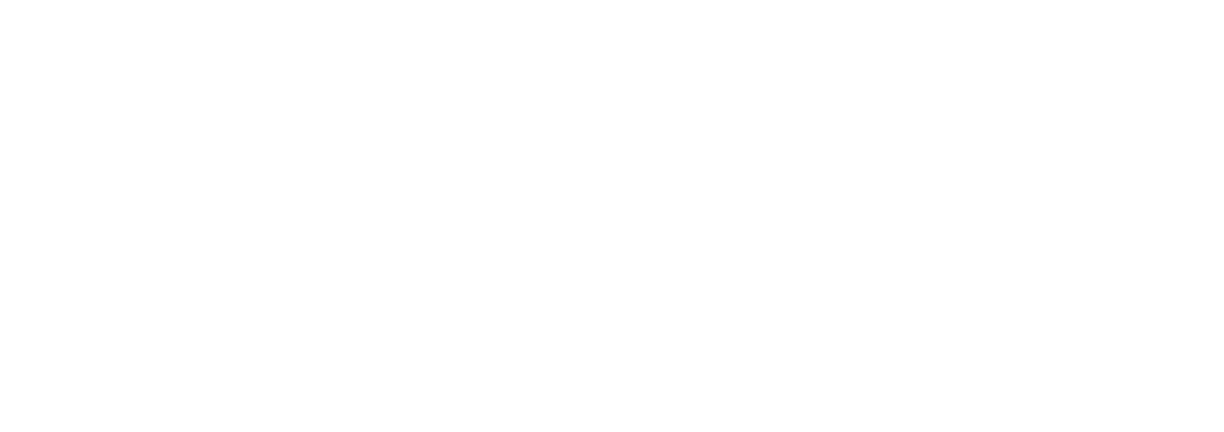